We are always thinking one step aheadConsulting, Engineering & Optimization in Logistics Networks
How can we help you?
Centralization to create synergy benefits for ERIKS
An interview with Laurens Verberne, Business Controller at ERIKS, by Marcel te Lindert
A sustainable light industrial facility is currently under construction alongside the motorway on the outskirts of the Dutch city of Ede. From 2020 onwards, this is where technical wholesaler ERIKS will be centralizing several departments including its Industrial Plastics business unit and a part of general sales. Groenewout supported the company during the design of the building and the search for a suitable property developer. Laurens Verberne, Business Controller at ERIKS: “Groenewout is our guarantee that the full program of requirements will be realized under the best possible property development and lease terms.”
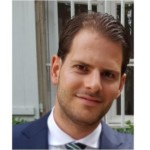
ERIKS supplies technical and mechanical components. It offers customers not only a wide choice of products, but also services and expert advice relating to all the components across its seven business units, one of which is Industrial Plastics. “In Industrial Plastics, we sell semi-finished products such as stock plates, round and hollow bars, but our added value lies in the further processing of those products,” says Laurens Verberne, Business Controller at ERIKS. “This ranges from first-line services such as cutting the stock plates, round and hollow bars to size, to third-line processing services in which we transform the semi-finished products into customer-specific components.”
The Industrial Plastics sales team is currently spread across four sites in the Netherlands: in Alkmaar, Ede, Eindhoven and Almelo. The majority of the company’s logistics activities, including the first-line services, are based in Eindhoven. “But almost 80% of our employees are based in Ede, which is where we perform the third-line multi-process services that require the use of several different machines. In addition, we have a facility in Almelo for quick-response manufacturing where we handle urgent orders with a maximum lead time of one week rather than the standard three weeks in Ede.”
Cutting down on locations
The idea to alter the existing four-location organizational set-up first emerged when the company outgrew itself in Ede. As a result of continual rapid growth of the third-line processing activities over many years, the activities are currently performed in five different buildings. The situation is far from optimal, explains Verberne: “There is a lot of extra internal transport. It’s not unusual for a forklift to have to cross two roads to fetch a component from another warehouse. That’s why we started thinking about a new-build project – initially only for our Ede operation, but we gradually realized that from a strategic perspective this was the perfect time to centralize all of our business unit’s activities. After all, we have a lot of internal transport between our four sites. Centralization would eliminate all that.”
But what’s the best way to go about centralizing the activities from four sites to just one? ERIKS turned to Groenewout for help. “We’re specialists in industrial plastics, not property development, so we searched for of a partner who could support us,” says Verberne. He talked to several consultancy firms before choosing Groenewout: “What we particularly liked about Groenewout was their mindset. ERIKS is a down-to-earth company with a hands-on approach, and Groenewout is very similar. It felt right immediately – and it was the right decision, since we are still working with them 18 months later.”
Some products of the assortment Industrial Plastics ERIKS
From building blocks to design
Groenewout started by conducting a feasibility study: first by preparing an overview of all the production steps and logistics processes, then taking stock of the complete machine park and all inventory, and lastly making forecasts: how much space will be needed for each production step in the future? “For example, one of the areas in Ede – the CNC milling department – currently takes up 100 square meters. But how much space will we need for that department if we keep growing as expected? 150 square meters or 200? That’s how we defined a number of building blocks as the basis for the new facility,” he continues.
They then looked at how to optimally arrange those building blocks. What would be the ideal sequence for the underlying production steps? “In effect, Groenewout analyzed our process flow and we used their findings as the basis for arranging the building blocks in the space. That resulted in a general outline indicating how big the building needed to be. An architect then translated it into the actual design for the facility, including the program of requirements drawn up by Groenewout in close consultation with us.”
The search for a property developer
So ERIKS went in search of a property developer who would be prepared to take on the new building. Groenewout coordinated that search in terms of both the technical and contractual aspects. “At Groenewout they know the market and how to talk to project developers. They also helped us to compare the various proposals fairly in terms of price, quality, speed of construction and contractual terms and conditions,” explains Verberne.
Artist impression ERIKS (source: Janssen Wuts)
Detailed development and lease contract
Groenewout has specialized experience in drawing up development and lease agreements. “That’s another thing we hardly ever do. They came up with a list of at least 25 details to consider; we would never have thought of them all ourselves. That resulted in a much better contract overall. The long-term contractual conditions are crucial for us – even more important than the rental price, in fact.”
In the contract, the emphasis is on the development and construction of the building and the associated risks and costs on the one hand, and on the completed facility and the mutually agreed rental conditions on the other. Because of the unique nature and the intended use of the facility, the final contract differs from the standard Dutch rental agreement (based on the ROZ model) on a number of points, mainly related to alteration, expansion and maintenance of the building.
Initially, Verberne was concerned that they would have to make too many concessions in their design. After all, a project developer is only interested in investing in a future-proof property with wide appeal, yet ERIKS had some very specific requirements. “One thing we did to give the building broader appeal was raise a part of the roof. But ultimately much of the original design remained unchanged, thanks largely to Groenewout.”
Robotized warehouse
ERIKS signed a contract with HVBM Vastgoed in April 2019, and construction work started in Ede just two months later. “We’re constructing a sustainable building, with a BREEAM Very Good rating, comprising 1,600 square meters of office space and 10,000 square meters of production and logistics space,” states Verberne. He expects the centralization to result in many synergy benefits, including a substantial reduction in the number of logistics movements and the need for much less stock. “Besides that, the new building gives us new opportunities for robotization. For example, we will have a fully robotized warehouse measuring 75 by 16 meters. The robots will pick the right material and subsequently place them on the processing machines fully automatically. That combination of expertise and robotization will be worth gold in the future.”
Groenewout is still involved in the new-build project; the consultancy firm attends every construction meeting to ensure that the program of requirements is delivered in full and that the development contract is adhered to as agreed. In the case of any discussions about alterations or deviations from the contract, ERIKS relies on Groenewout’s advice. “We’re very happy with their support. They have the knowledge and experience that we lack. Besides that, they’re flexible and we can contact them at any time. It’s never a problem if we have to discuss something out of office hours. It’s no coincidence that another business unit within ERIKS has since hired Groenewout for a new project.”
Text by Marcel te Lindert
Marcel te Lindert is a journalist with over 20 years of experience in the logistics industry. He was editor-in-chief of the Dutch magazines Transport+Opslag and Logistiek. Nowadays he works freelance for trade magazines including Supply Chain Magazine and Warehouse Totaal.
More information
If you would like more information about this project, please contact Mari van Kuijk, vankuijk@groenewout.com, or call tel. +31 76 533 04 40. For more information about ERIKS, see www.ERIKS.nl